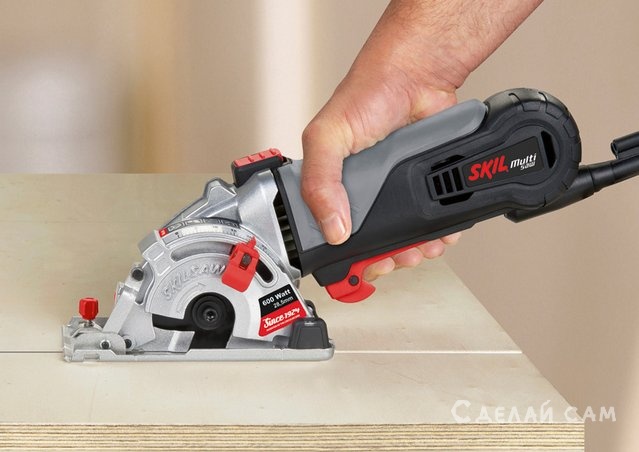
Участвуй в конкурсе с 8 апреля до 15 мая и выиграй один из инструментов Skil!
Недавно ко мне в руки попали 2 замечательных инструмента, а точнее мне их прислали из компании Skil, которая входит в холдинг Bosh и попросили дать оценку данным инструментам.
Речь идет о ручной универсальной пиле Skil saw multi. Это компактная пила для резки различных материалов Skil 5330 LA (Multisaw) и зачистной инструмент для краски Skil 8100 LC (Tornado)
Вот фото Skil multisaw и Skil Tornado:
Оба инструмента очень качественно сделаны и в руках их держать очень приятно. Прорезиненный пластик. Эти инструменты удобно держать при работе.
В этом обзоре начнем с пилы Skil multisaw:
Эта достаточно мощная пила предназначена для пиления дерева, фанеры, пластика, керамики, алюминиевого профиля и мы даже пилили оцинкованный стальной лист.
- Мощность двигателя: 600 Вт;
- Диаметр диска: 89 мм;
- Диаметр посадочного отверстия: 10 мм;
- Макс. глубина пропила под углом: 90°:28.5 мм;
- Скорость без нагрузки: 6000 об/мин;
- Наличие системы пылеудаления: есть;
- Вес: 2 кг;
- Легкая компактная конструкция облегчает работу одной рукой, обеспечивая тем самым оптимальную свободу движения.
В комплект пилы входят 3 круга, 2 одинаковых, которыми можно пилить пластик, дерево, алюминиевый профиль и третий круг - алмазный - для керамики, камня и т. п. материалов.
Также в комплекте имеется шланг для подсоединения пылесоса, специальный упор, для резки материалов определенной ширины (максимум 12 см), шестигранник, инструкция и гарантийный талон.
Официальный сайт skil: http://www.skileurope.com/ru/ru/diyocs/
Вот видео моего обзора данной пилы:
После чего пила была испробована в работе. Пилили алюминиевую гардину ) но не просто так, а чтобы ее использовать в качестве правила под батареей, когда делали стяжку для теплых полов.
Пила показала себя с очень хорошей стороны!
Потом распустили оцинкованный лист для коньков на крыше дома. В общем сложности распилили 12 метров оцинковки и 1.2 метра алюминия.
Проверили зубцы на диске - они не сработались. Можно еще пилить и пилить.
Вы можете посмотреть видео наших испытаний!
В общем рекомендую эту пилу. Она всегда пригодится в домашнем хозяйстве.
Если у вас появились вопросы по этому инструменту - пишите, я отвечу. Может еще сниму видео о том, как пилить другие материалы.
А если вы сами обладатель такой пилы, то попрошу высказать свое мнение и дать ценные советы по её использованию!
Шлифовальная машина Skil 8100 LC (Tornado)
Общие характеристики:
Потребляемая мощность: 550 Вт.
Макс. частота вращения диска: 2600 об/мин
Макс. диаметр диска: 125 мм
Резьба шпинделя: M14
Питание: от сети
Возможности: фиксация шпинделя, блокировка кнопки включения
Дополнительная рукоятка: есть
Кейс в комплекте: есть
Вес: 1.8 кг
Комплектация: полировальный диск, шлифовальная подошва, ключ, комплект фланцев, суконный круг, наждачный круг, сумка
Шлифовальная машина идеально подходит для новичков и для тех кто уже работал с данной техникой. Удобное для работы под разным углом. Инструмент качественный и надежный.
Skil 8100 LC питается от сети, что значительно увеличивает использование его в повседневных условиях работы, не требуется подзарядка аккумуляторов. Считаю, что инструмент должен работать от бесперебойного источника питания и в процессе работы не даст сбой, в отношении заряда аккумулятора. Уверенное использование шлифовальной машины - гарантия высокого качества и количества выполненной работы.
Если у кого имеется данный аппарат, прошу высказать свое мнение и замечания. От себя хочу добавить, что у каждого самодельщика должен быть инструмент высокого качества, а в особенности шлифовальная машина пригодится в любом случае.
- Блог пользователя - Антон
- Войдите, чтобы ответить
- 9620 просмотров